The Ultimate Guide to Cross-References
An in-depth guide on electronics cross-references and the best practices for finding the best cross components.
Using Advanced Search for Electronics Cross-Reference
With so many details to assess and constant design modifications and part obsolescence events, searching for component crosses can be time-consuming and susceptible to human error. Z2Data's Park Risk Manager allows you to readily view form-fit-function crossings from many vendors or replacements from the same provider by simply searching for any MPN.
Supplier, family data, cross-grade, lifecycle, price, lead time, market availability, component score, parametric characteristics, and more may all be compared on a single platform through Z2Data.
The advanced search through Part Risk Manager provides accessible information and analyzes cross-references on all parts through the scope of different drop-in grades. These drop-in grades define how easily one electronic or mechanical part may be used in the place of another part. Find out more about drop-in grades in our next section.
When you need to search for a part, Z2Data enables you to search by:
- Part Number
- MPN
- IPN
- Family
- Description
- Supplier
- And more
Flexibility is critical during a cross-component selection process, but it is also important to ensure you are finding the best crosses for your electronics company.
How to Find the Best Cross-Components
Cross-references are instantly found by engineers at prominent OEMs without the need to open a single datasheet. How? They employ comprehensive services such as Z2Data to gain access to data on over 1 billion electrical/mechanical components. Part Risk Manager makes it simple for businesses to obtain the most precise cross-references.
They may analyze form-fit-function, use sophisticated comparison tools, verify availability, and discover alternatives from the same supplier, all of which will help them improve the efficiency of their cross-reference selection operations.
Let’s take a look at the best practices in finding the most accurate cross components:
1. Evaluate the Form-Fit Function
A crossing part's form-fit function must be equal—or at least acceptable—to the original electronic part. Here's a short breakdown of what each facet of form, fit, and function entails:
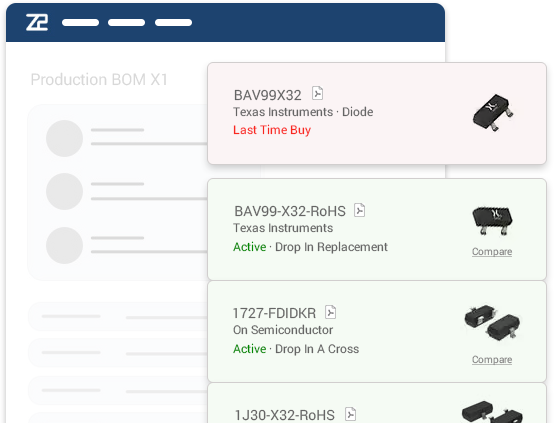
- Form: the visual parameters of a part such as the shape, size, mass, weight, and dimensions.
- Fit: a part's ability to interact, interface, or connect to another part.
- Function: the part's ability to perform an intended function.
We make it simple to grasp the varying degrees of similarity between cross-references at Z2Data. This is accomplished by grading crosses on a scale of A to C.
- Drop-In A: All crosses that have the same package and pinout with no differences in parametric features.
- Drop-In B: All crosses that have the same package and pinout with minor differences in parametric features.
- Drop-In C: All crosses that have the same package and pinout with major differences in parametric features. Using drop-in grades makes it much easier to evaluate form-fit-function for different cross-components.
Once you’ve found the best drop-in part, another best practice is to ensure the manufacturer of the new, cross-component is stable and reliable. After all, you don’t want to be looking for another cross-reference in the coming months because the manufacturer for your new component is unreliable or has gone out of business.
2. Assess Manufacturer Stability
When choosing crosses, keep the part manufacturer's stability in mind. Part Risk Manager gives information on a manufacturer's goods, compliance, locations, supply chain, top customers, distributors, acquisitions, and detailed financial history. All of this information assists you in ensuring that the manufacturer can continue to operate its business in the long run.
Many firms may believe that by evaluating their suppliers, they have considered all factors of risk. However, even when onboarding is complete, it is vital to continue to check your suppliers' financial, operational, and legal health. To remain on top of suppliers, you can browse the internet or phone them for weekly updates. But this takes a lot of time and effort. Instead, Z2Data provides a single source to access critical supplier profiles. This data enables you to keep track of the supply chain's "big picture" manage supplier and distributor relationships and re-evaluate supplier risk in real-time.
Having rapid access to detailed supplier profiles can contribute to a major comparative advantage in crises such as natural disasters and recovery scenarios. A trusted, stable supplier means you have a steady supply of critical components and less time wasted looking for new crosses.
Each supplier profile covers data points on:
- Supplier Financials
- Portfolio of Top Products
- Distributors
- Competitors/Customers
- Manufacturing Locations
- Supply Chain
- And more
If you’ve narrowed your search down to a shortlist of parts, you don’t want to have to constantly flip through different data pages to compare parametric details. With Z2Data, you don’t have to.
3. Use Side-by-Side Comparisons
Part Risk Manager offers side-by-side comparisons for insightful assessments. You can also filter by differences and similarities to make the evaluation process even more efficient.
With Z2Data, you would see comprehensive information comparing each part's:
- Part Risk Score
- Company Risk Score
- Datasheet
- Introduction Date
- Replacements and crosses count
- Package Dimensions
- Parametric Data
- Risk of Obsolescence
- Market Availability
- Pricing and Lead Times
- Compliance
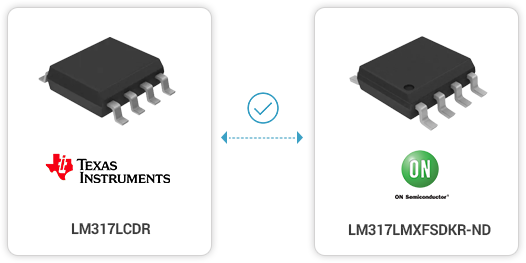
Don't waste hours, if not days, waiting for cross-reference information from manufacturers, EMSs, and distributors. Use a cross-referencing tool, such as Z2Data's Part Risk Manager.
The Difference Between Proactive and Reactive Cross-Reference Management
After an unforeseen obsolescence event, your company can be left scrambling to find a cross-component in order to avoid a refresh or redesign.
Choosing to be proactive about cross-referencing might be tough. So far, being reactive has worked for many businesses. A reactive strategy, on the other hand, is analogous to holding a metal rod in a rainstorm and praying that lightning does not strike.
What a Reactive Cross-Reference Approach Looks Like
Consider how your company handles cross-referencing. When you obtain a PCN from a supplier or manufacturer, you go out and locate replacement parts. You wait to be alerted about the end of life of a part before looking for a replacement. You learn of a supply scarcity and are forced to seek out a cross that can match the form-fit function of your original part. You're waiting for the problem to come to you in all of these scenarios.
Human nature is characterized by ad hoc or reactive methods. We are naturally predisposed to seek answers only when issues emerge. While this is a natural approach, it is also one that is reactive. Everything is OK with a reactive attitude... until it isn't. And it only takes one nightmare, such as missing an LTB (last time buy), for a corporation to reassess its ad hoc inclinations.
How to Create a Proactive Approach to Cross-Referencing
1. Keep cross-references on-hand
There were 1,069 supply chain interruptions in the first half of 2018. This is a 29 percent increase since 2010 and a 10 percent increase since 2016. The availability of your parts becomes less reliable as supply chain disruption incidents occur.
Take a proactive approach by compiling a list of crosses that your team can use as a backup. This ensures that you will always have a replacement on hand if one is required. Remember that creating a list of crosses is simple using Z2Data's Part Risk Manager.
2. Anticipate PCNs and PDNs by planning for lifecycle events
The Part Risk Manager from Z2Data assesses each part's expected obsolescence year. With these insights, parts with early expected obsolescence years are assigned greater risk ratings, and your team can begin to search for crosses on high-risk parts.
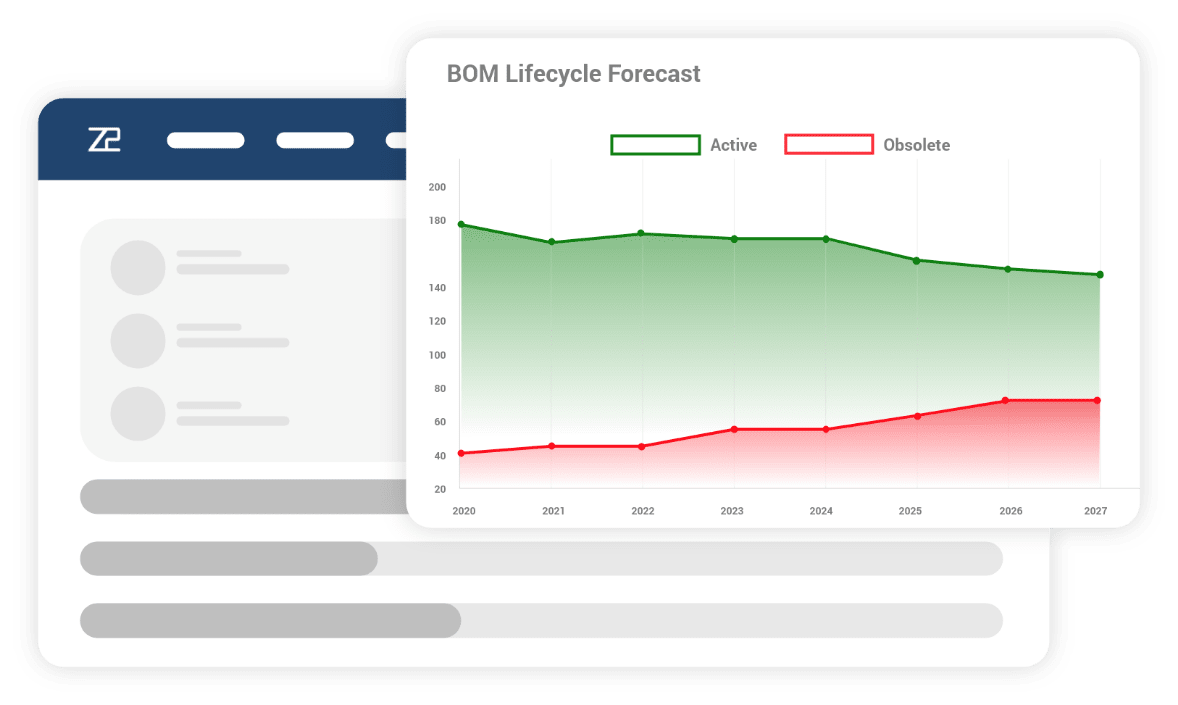
Evaluating and anticipating lifetime events prior to the issuance of PCNs allows your enterprise to establish cross-references for obsolescence events that occur months, if not years, in the future.
3. Consider future designs
Create prospective goods with adaptability in mind. Not all crossings will conform to the precise form-fit function of your existing components.
Use Part Risk Manager's extensive database to find adaptable components with many crossings. This way, you may avoid future redesigns if one of your parts becomes obsolete but has a large number of viable replacements.
Z2Data's Part Risk Manager assists your firm in maintaining a proactive approach to cross-referencing and obsolescence management by generating a list of replacements, anticipating PCNs and PDNs with lifespan estimates, and appraising components for future designs.